GERMANY. Leading travel retailer and distributor Gebr. Heinemann today marks 20 years of operations at its Hamburg-Allermöhe logistics centre, which is a crucial element in the company’s supply chain.
The Hamburg-based family-owned company said that the “the combination of continuity and innovation still sets a benchmark in the travel retail logistics sector”. The Allermöhe centre was supplemented in 2014 by another highly automated logistics centre in Erlensee near Frankfurt, with regional warehouses in Norway, Miami and Sydney, among other locations.
Gebr. Heinemann is celebrating the 20th anniversary in Allermöhe with a party for current and former employees.
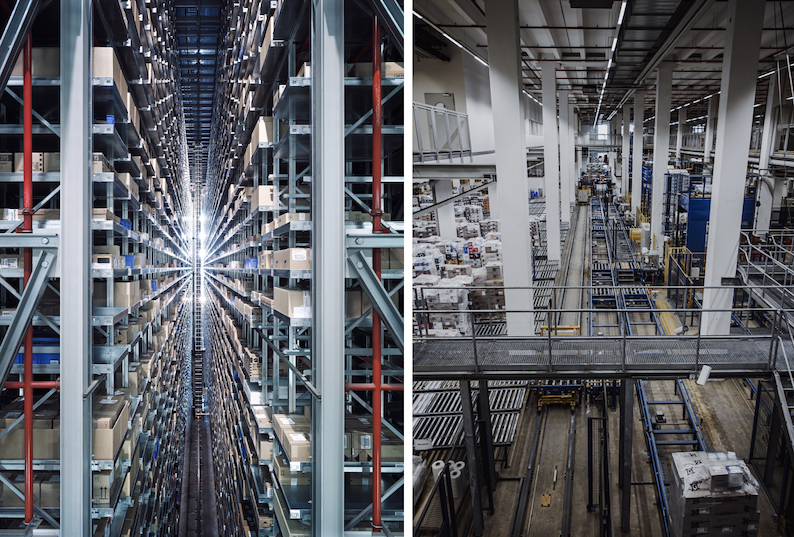
From small beginnings…
On 19 May 2003, the highly automated central logistics centre in Allermöhe began operations after two and a half years of construction.
The foundation of the 16,000sq m space was anchored to 1,000 piles driven to a depth of up to 12 metres. The opening was a milestone for Gebr. Heinemann, as it was the first time the company became the owner of a self-built warehouse property outside the Hamburg free port, and was the largest investment in the company’s history. Through the gradual relocation of all product groups to Allermöhe, previously used storage locations were dissolved.
Three years after the opening came the extension of a high-bay warehouse, with additional office space developed in 2014. This meant an additional 18,000 pallet storage spaces and 36,000 tray storage spaces or an extension of the existing storage space by +66%. This created the space and conditions to meet the growing demands of the travel retail market, said Gebr. Heinemann.
People: the central factor for success
“The truly outstanding component of the success of our logistics centre is the people who make up the heart of Allermöhe,” said Director Logistics Martin Borscheid.
“Of the 350 people employed here today, 67 have been with us from the beginning, and many have been part of the Heinemann family for 20 years or more. The experienced teams are optimally complemented by new employees for our joint path into the future.
“Qualified specialists are in demand because although processes are continuously improved, specialist knowledge is necessary to ensure the often difficult handling of goods. Our logistics is particularly unique in the global travel market because nowhere else can you get everything from a single source, from the perfectly stored cigar to a €45,000 whiskey and an elegant Bulgari ring.”
The logistics centre is constantly being improved with innovative technical solutions and modern ergonomic workspaces, said the company.
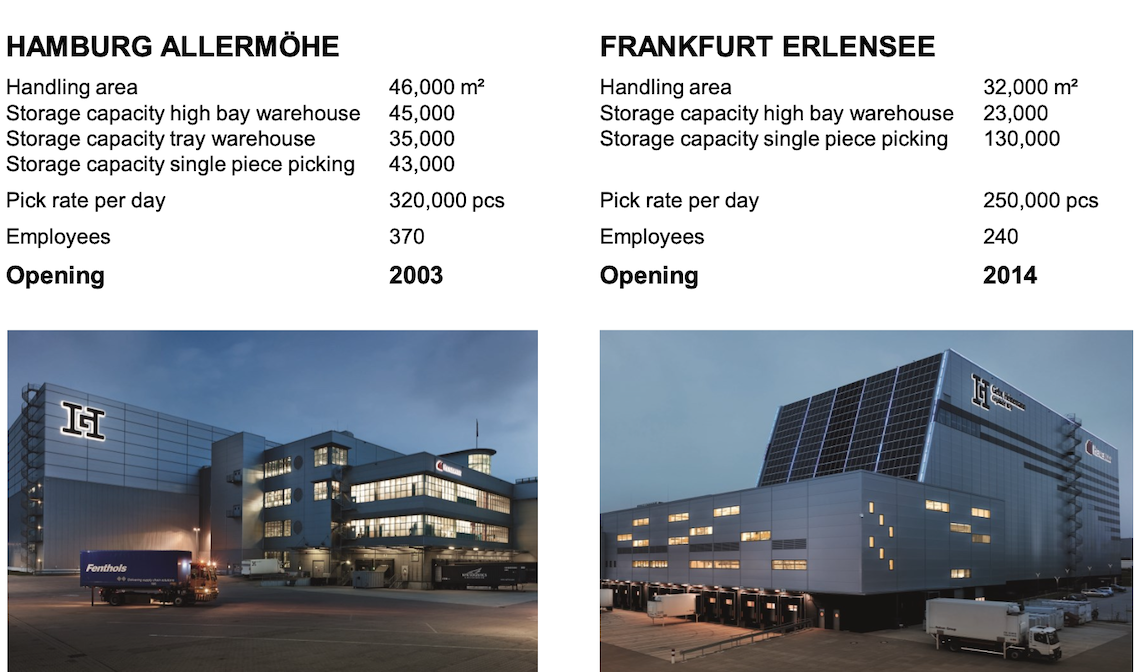
“The retrofit approach, this means the continuous modernisation and updating of existing plants and equipment, ensures that the systems are always state-of-the-art and equipped with intelligent solutions for the challenges of the future. It is crucial to carry out the replacement without disrupting ongoing operations,” said Borscheid. Innovative solutions currently being implemented include, for example, ‘Google Glasses’, a picking glass with an attached finger scanner.
Other innovative processes introduced over recent years include Secure Supply Chain [EU-patented LOGseal], Secured Automated Guided Vehicles, Exoskeletons for staff and Forklift Fleet Management.
Ambitious sustainability targets
“We want to be carbon-neutral by 2030,” said Vice President Supply Chain Inken Callsen. She said: “In April, we invited our transport partners to a Sustainability Summit to find solutions to reduce CO2 emissions together. We have already achieved a lot and were able to reduce emissions by -9% in 2022 compared to 2019. This year, we aim to achieve another -6% reduction in order to reach our goal of -25% savings in 2024 compared to 2019.”
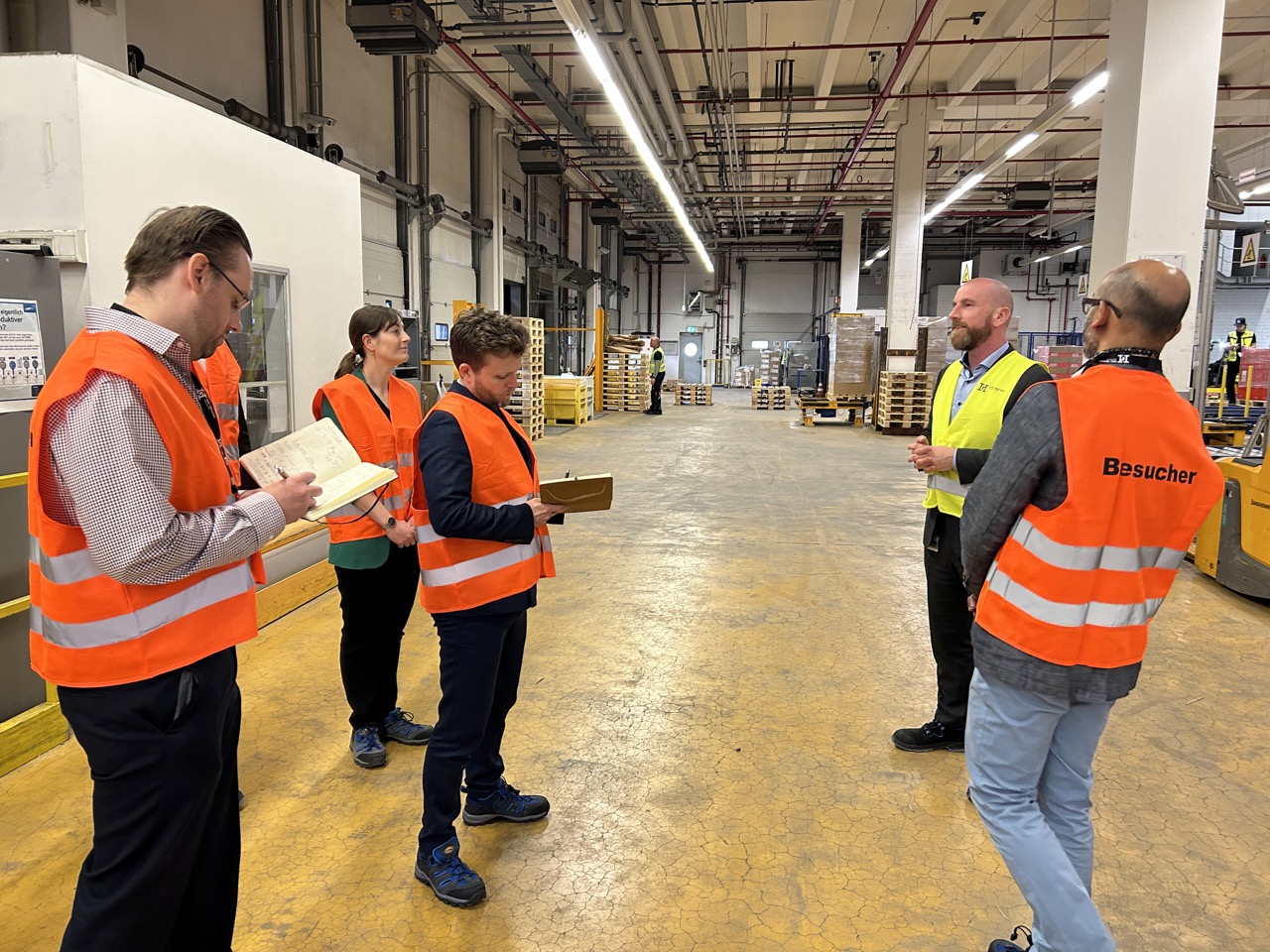
Media guests to Gebr. Heinemann’s press conference on 27 April paid a visit to the logistics centre on the day. Addressing the key elements of successful operation, Inken Callsen said (in a video message): “We stand on three pillars: supply chain performance, collaboration and a flexible, sustainable network.”
Supply chain performance is about product availability, time to market, cost efficiency and automation, taking a customer-centric approach that allows service “to be the best in the market”, Callsen explained.
On collaboration, this means partnership and joint forecasting with suppliers to lean on the combined knowledge of each party.
The flexible, sustainable network means having the shortest route to market and making as many CO2 savings where possible. Opening the N-Hub or Norwegian Hub was one answer to this challenge, ensuring delivery from inside a 10km radius to the shelves of stores at Oslo Airport.
Martin Borscheid, Head of Supply Chain Strategy & Effectiveness Laura Moser and Floor Manager In-/Outbound Folke Montgomery built on these points on a tour with media guests.
Moser said that priority areas today include the continuation of master data management cooperation (begun in 2018) and collaboration on forecasting with leading partners. “We are the only ones who send a six-month forecast to our suppliers, which enables influence their production in in turn helps us receive the goods we order. Last year we improved the on time and full quota from our suppliers by six percentage points. This supports our delivery of a good supply chain experience.”
Automation is key too. Robot processing automation has been a big element, with many thousands of manpower hours saved through recent initiatives.
Moser added: “We want to make supply chain performance the best it can be to ensure the best possible experience for our customers. We look at the efficiency of what we do in our network, and ensure that we are reliable, resilient and ready for scalable opportunities.
“That also means being sustainable with less carbon footprint and more efficiency.” Recent examples include electric trucks, and more local hubs such as the N-Hub in Oslo, which have delivered big savings on energy and time to market, and allows the company to be more flexible and resilient in its network.
Martin Borscheid added: “With our hubs we have partners operating around the world from Sydney and Singapore to Miami and more are coming. We are ahead on logistics and aim to maintain that leadership.
Chief Commercial Officer Dr. Dirk Schneider added: “We must continue to meet the high demands on logistics with regards to performance, sustainability, and cost efficiency. Equally important is ensuring that we can respond flexibly to capacity adjustments and resilience requirements at any time.”
*Click here for our review of Gebr. Heinemann performance in 2022, as revealed at its 27 April press conference.